Become a Part of the NIKE, Inc. Team
NIKE, Inc. does more than outfit the world’s best athletes. It is a place to explore potential, obliterate boundaries and push out the edges of what can be. The company looks for people who can grow, think, dream and create. Its culture thrives by embracing diversity and rewarding imagination. The brand seeks achievers, leaders and visionaries. At NIKE, Inc. it’s about each person bringing skills and passion to a challenging and constantly evolving game.
WHO YOU’LL WORK WITH
The Manufacturing System Engineer is a pivotal role within Nike’s manufacturing engineering team, responsible for driving the development and implementation of foundational capabilities in Lean, Product Quality, Industrial Engineering, and Garment Engineering. This position will support Nike’s strategic manufacturing initiatives.
WHO WE ARE LOOKING FOR
What You Bring
- A minimum of 3 years of experience in Manufacturing Systems Engineering, with a strong foundation in Quality, Lean, Industrial Engineering, and Garment Engineering.
- Excellent communication and collaboration skills, with the ability to work effectively across different teams and organizational levels.
- Proficiency in process engineering and data analysis, with a track record of successful process improvement and optimization projects.
- A solid understanding of manufacturing technologies and their application in enhancing operational efficiency and quality.
- Experience in implementing and sustaining Continuous Improvement methodologies such as Lean Manufacturing and Six Sigma.
- A bachelor’s degree in industrial engineering, Manufacturing Engineering, or a related field; advanced degree or certifications are preferred.
Desired Attributes:
- A results-driven mindset with a focus on operational excellence and continuous improvement.
- Strong analytical and problem-solving skills, with a passion for optimizing manufacturing processes.
- A commitment to quality and continuous improvement, with a passion for innovation and excellence.
- The ability to meet factory engineering and leadership teams in-person and represent Nike, inc.
- The ability to inspire and guide internal and external teammates towards achieving common objectives and fostering a culture of innovation.
- A commitment to staying current with industry best practices and emerging technologies in manufacturing systems engineering.
- Excellent organizational and project management skills, with the ability to manage multiple projects simultaneously.
- Work from WHQ. Not a remote job.
- Ability to travel 25% of your time within factory locations in the North America continent.
WHAT YOU’LL WORK ON
Your Main Responsibilities
- Support and implement Quality, Lean, Industrial Engineering, and Garment Engineering principles within Nike’s manufacturing partner base to elevate their overall capabilities.
- Collaborate with the senior managers, Manufacturing System Engineering and Advanced Manufacturing Engineering teams to align and drive Nike’s strategic manufacturing goals, continuous improvement objectives, and to support the delivery of high-quality products while maintaining manufacturing efficiency within production.
- Collaborate with Nike’s Product Risk Engineering team (based in World Headquarters) to deploy Nike’s product performance standards and lead the standardization of manufacturing processes, ensuring consistency and efficiency across Nike’s APAC partner base.
- Manufacturing Readiness: Leverage manufacturing integration, engineering tools, and best practices with quality/process engineering to mitigate risk at production.
- Manufacturing Execution: Operate with world-class production quality engineering processes to assure perfect product is made right at the first time.
- Inspections & Audits: Reference quality measurement and verification of post-production materials and product, to make informed product decisions.
- Issues Management: Support Nike’s Issues Management team to conduct comprehensive review, analysis, and resolution of product issues.
- Data Analysis: Establish and track performance metrics to assess the impact of implemented initiatives on manufacturing outcomes.
- Project Management: Establish clear accountability from internal and external stakeholders to deliver against our key objectives.
We offer a number of accommodations to complete our interview process including screen readers, sign language interpreters, accessible and single location for in-person interviews, closed captioning, and other reasonable modifications as needed. If you discover, as you navigate our application process, that you need assistance or an accommodation due to a disability, please complete the Candidate Accommodation Request Form.
OUR HIRING GAME PLAN
01 Apply
Our teams are made up of diverse skillsets, knowledge bases, inputs, ideas and backgrounds. We want you to find your fit – review job descriptions, departments and teams to discover the role for you.
02 Meet a Recruiter or Take an Assessment
If selected for a corporate role, a recruiter will reach out to start your interview process and be your main contact throughout the process. For retail roles, you’ll complete an interactive assessment that includes a chat and quizzes and takes about 10-20 minutes to complete. No matter the role, we want to learn about you – the whole you – so don’t shy away from how you approach world-class service and what makes you unique.
03 Interview
Go into this stage confident by doing your research, understanding what we are looking for and being prepared for questions that are set up to learn more about you, and your background.
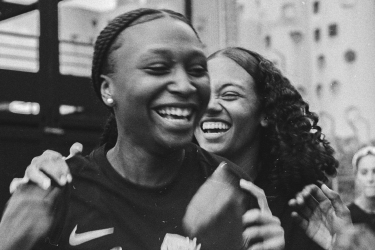