Become a Part of the NIKE, Inc. Team
NIKE, Inc. does more than outfit the world’s best athletes. It is a place to explore potential, obliterate boundaries and push out the edges of what can be. The company looks for people who can grow, think, dream and create. Its culture thrives by embracing diversity and rewarding imagination. The brand seeks achievers, leaders and visionaries. At NIKE, Inc. it’s about each person bringing skills and passion to a challenging and constantly evolving game.
Senior, Manufacturing Systems Engineer (Apparel & Accessory)
WHO YOU’LL WORK WITH
This role reports to the Senior Manager, Manufacturing Systems Engineer in South Asia and closely collaborates with the Product Risk Engineering, based in World Headquarters (WHQ), Manufacturing Systems Engineering, and Advance Manufacturing Engineering teams to align and drive Nike’s strategic manufacturing goals and continuous improvement objectives and to support the adoption of advanced manufacturing technologies that enhances foundational capabilities and connect the dots.
WHO WE ARE LOOKING FOR
We’re looking for a Senior Manufacturing Systems Engineer based in Ho Chi Minh City, Vietnam. This is a key role within Nike’s Manufacturing Engineering team, responsible for driving the development and implementation of foundational capabilities in Quality, Lean, Industrial Engineering, and Garment Engineering, leading and ensuring alignment with Nike’s strategic manufacturing initiatives.
Minimum 3 years of experience in Manufacturing Systems Engineering, with a good foundation in Quality, Lean, Industrial Engineering, and Garment Engineering.
Bachelor’s degree in industrial engineering, Manufacturing Engineering, or a related field; advanced degrees or certifications are preferred.
Proven leadership and management skills with the ability to inspire teams, manage multiple projects, and drive innovation.
Good communication and collaboration skills, working effectively across teams and organizational levels.
Thorough understanding of apparel/accessory manufacturing processes, including scheduling, manufacturing, and distribution, with a focus on product and service quality.
Knowledge of manufacturing technologies and their application in enhancing operational quality and efficiency.
Ability to prioritize, direct teams/projects, and ensure timely completion while working with all levels of management and different partner groups.
A fair understanding in implementing and sustaining Continuous Improvement Methodologies such as Lean Manufacturing and Six Sigma. A result-driven mindset with a focus on operational excellence, use data to influence decision making and drive continuous improvement.
Good analytical and problem-solving skills, with a passion for optimizing manufacturing processes and familiarity with Microsoft Office and data analysis tools.
Proficiency in process engineering, with a track record of successful process improvement and optimization projects and proficiency in General Sewing Data (GSD) and background in factory capacity planning & management is a plus.
WHAT YOU’LL WORK ON
In this role, you will drive manufacturing excellence by developing, standardizing, and optimizing manufacturing processes across Nike Apparel and Accessory (APAC) partner network. Key responsibilities include:
Leadership: You will take the initiative to develop and implement Quality, Lean, Industrial Engineering, and Garment Engineering principles within Nike’s manufacturing partner base to elevate their overall capabilities.
Standards: You will liaise with Nike’s Product Risk Engineering team to deploy Nike’s product performance standards and lead the standardization of manufacturing processes, ensure consistency and efficiency across Nike’s APAC partner base.
Manufacturing Readiness: You will leverage manufacturing integration, engineering tools, and best practices with quality/process engineering to mitigate risk at production.
Manufacturing Execution: You will operate with world-class production quality engineering processes to ensure the perfect product is made right the first time.
Inspections & Audits: You will reference quality measurement and verification of post-production materials and products, to make informed product decisions.
Issue Management: You will collaborate with Nike’s Issue Management team to conduct comprehensive review, analysis, and resolution of product issues; you will lead the root cause investigation and Corrective and Prevention action (CAPA) follow-up for continuous improvement at the factory and build a culture of quality.
Marketplace Feedback: You will incorporate consumer feedback based on in-market product quality, and lessons applied to future product/manufacturing improvements.
As part of the role, you will establish and track performance metrics to assess the impact of implemented initiatives on manufacturing outcomes.
At Nike, we're committed to providing a fair and transparent application process for all applicants. Nike does not charge candidates any fees for recruitment or applications.
OUR HIRING GAME PLAN
01 Apply
Our teams are made up of diverse skillsets, knowledge bases, inputs, ideas and backgrounds. We want you to find your fit – review job descriptions, departments and teams to discover the role for you.
02 Meet a Recruiter or Take an Assessment
If selected for a corporate role, a recruiter will reach out to start your interview process and be your main contact throughout the process. For retail roles, you’ll complete an interactive assessment that includes a chat and quizzes and takes about 10-20 minutes to complete. No matter the role, we want to learn about you – the whole you – so don’t shy away from how you approach world-class service and what makes you unique.
03 Interview
Go into this stage confident by doing your research, understanding what we are looking for and being prepared for questions that are set up to learn more about you, and your background.
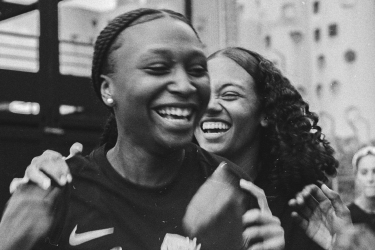